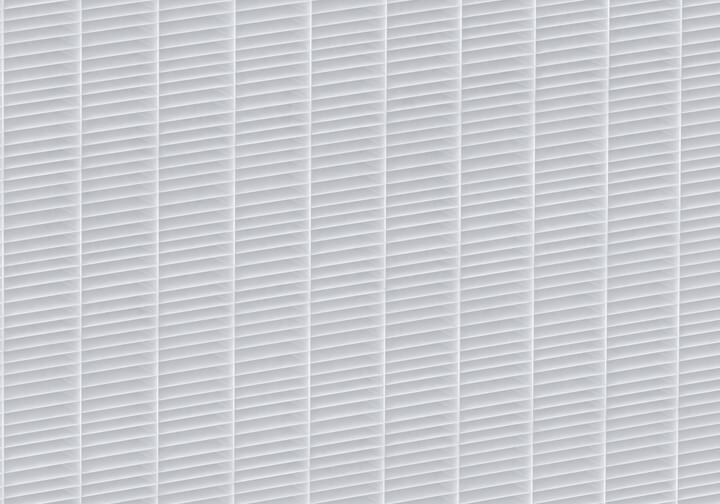
Our Process
Seven Steps to Custom Filters Optimized For Your Application and Equipment
We manufacture custom filters designed to fit your application and filtration equipment. These air filters are constructed of flame-retardant fiberglass paper that is pleated to increase the surface area for lower pressure drop and optimized filtration without compromising equipment productivity. For an additional safety measure, fire retardant glue and potting are also utilized.
Custom filter orders go through a simple 7-step process. Approximate lead time varies depending on the speed of the approval process, but is generally 4-6 weeks for delivery of the first order. Subsequent orders of the same product typically take 1-2 weeks.
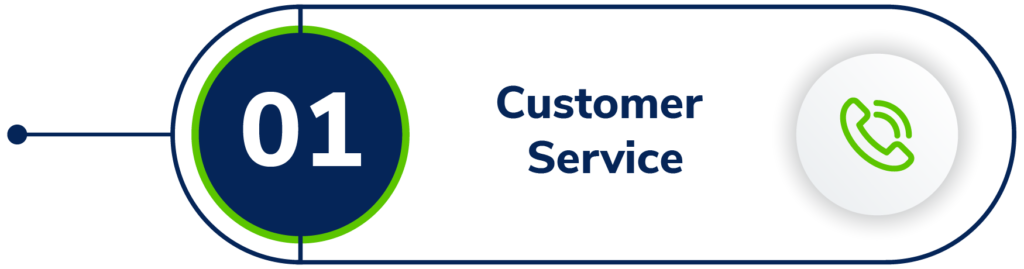
Customer Service
Discuss with the customer their application and requirements. Make recommendations and agree upon the desired filter. Place order.
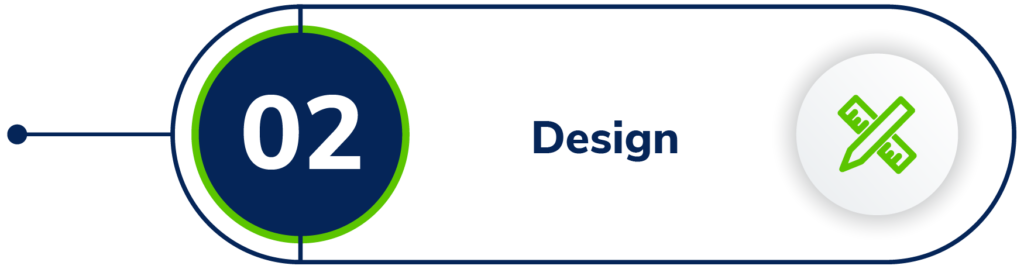
Engineering Design Service
Using the customers specs, create an engineering drawing. Work with the team to make adjustments, improvements and revisions.
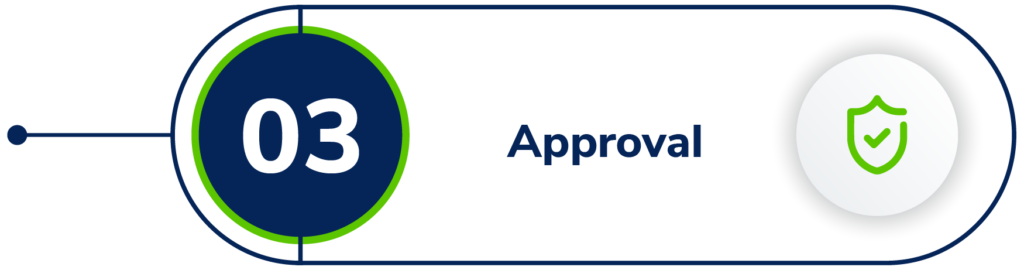
Customer Approval
Present the drawings to the customer for any modifications and review. Continue this process until customer accepts and approves the drawings.
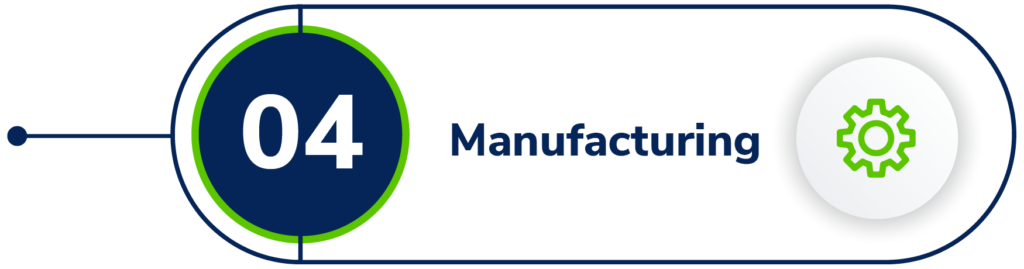
Manufacturing
Using our in-house, high quality machinery, build the filter to the engineering design.
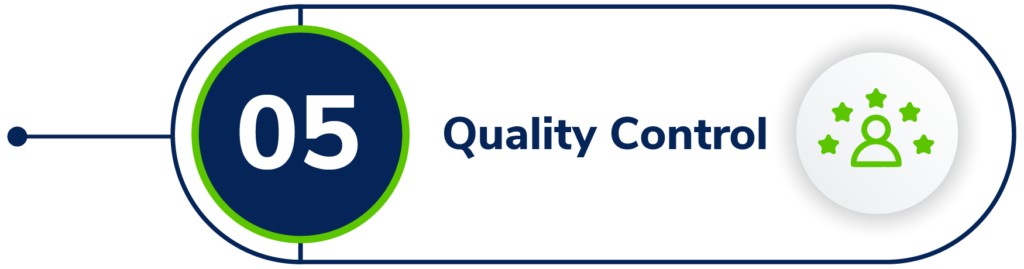
Quality Control
Our production team visually inspects each custom filter to meet high-quality standards.
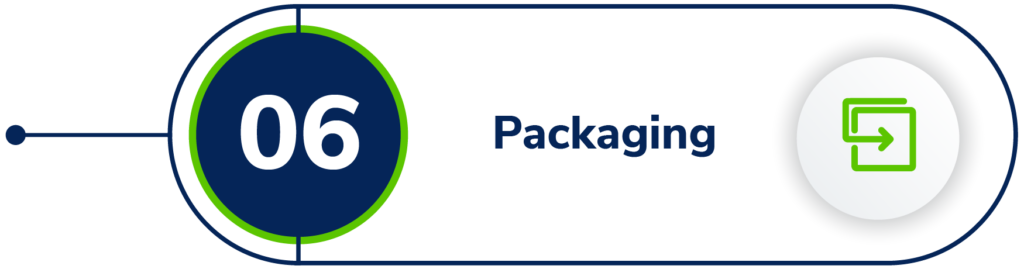
Packaging
Using quality packaging materials, professionally box filter(s) to ensure damage free transport.
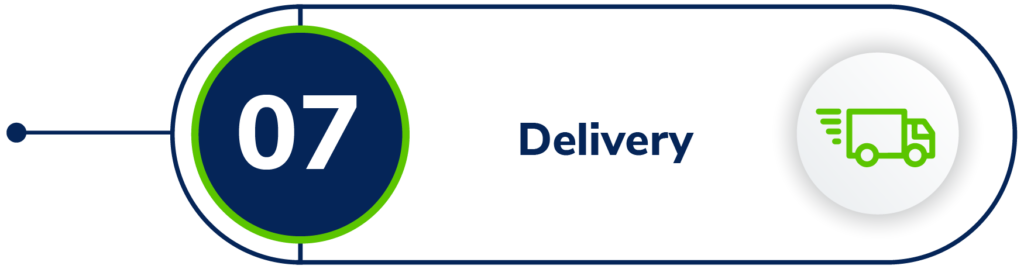
Delivery
With quick turn-around times, our in-house manufactured filters will ship from our Houston-based facility within weeks to assure on-time delivery.